MP & JP International Consultancy
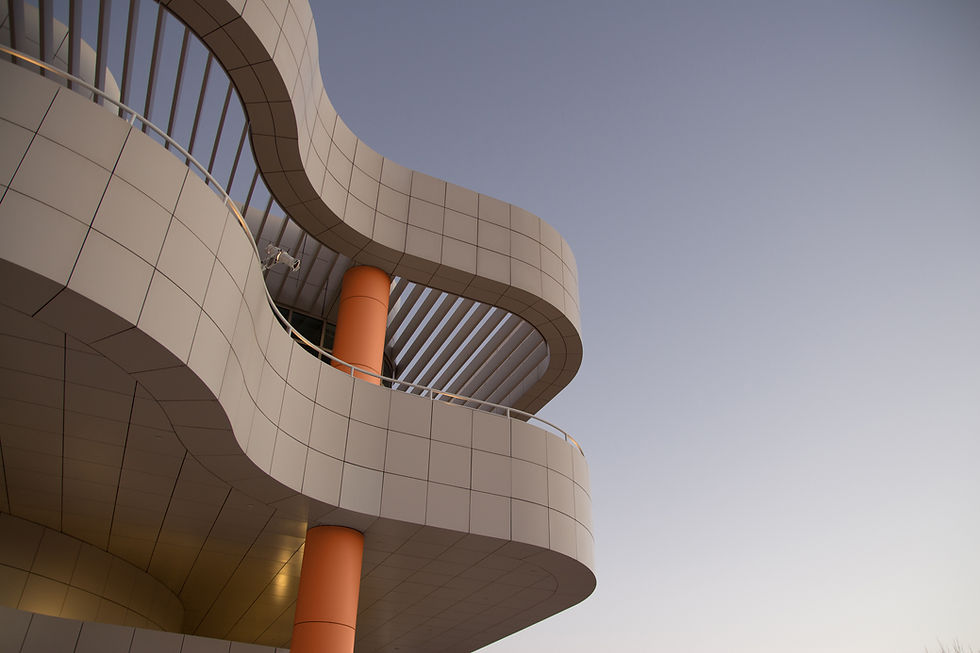
Utilizing Statistical Process Control (SPC) to Enhance Professional Quality Control Standards
Dec 3, 2024
5 min read
0
16
0
Statistical Process Control (SPC) is not just a technical term; it’s a vital approach that can transform the quality control landscape in any organization. Originating in the early 20th century, SPC has grown from its manufacturing roots to play a crucial role in industries like healthcare, finance, and services. This article will explore the fundamental principles of SPC, the benefits it brings, and how to apply it effectively in your organization.
What is Statistical Process Control (SPC)?
Statistical Process Control is a powerful method for monitoring and controlling processes using statistical techniques. By analyzing variations within a process, organizations can uncover areas needing improvement.
SPC focuses on reducing variability, which leads to consistent outputs and enhanced operational results. Common tools used in SPC include control charts, process capability analysis, and design of experiments, all of which support effective and data-driven decision-making.
History of SPC
SPC’s foundation lies in the pioneering works of quality leaders like Walter A. Shewhart, W. Edwards Deming, and Joseph Juran. In the 1920s, Shewhart developed control charts, a breakthrough that became essential to quality control.
Deming introduced these practices to Japan after World War II, significantly impacting the rise of quality circles and continuous improvement. SPC has since advanced, adopting sophisticated statistical methods and technologies that bolster its effectiveness.
Key Concepts of SPC
SPC comprises several essential concepts, including:
Variability
Variability refers to the differences present in any process. It can be categorized into:
Common Cause Variation: Naturally occurring differences that are part of the process.
Special Cause Variation: Variations introduced by external factors.
Control Charts
Control charts are visual tools that exhibit how a process behaves over time. By plotting data points and setting control limits, organizations can monitor stability and detect trends that may need attention. For instance, a manufacturing plant might use control charts to monitor daily production levels, identifying any outliers that could indicate a problem.
Capability Analysis
Process capability evaluates how well a process meets its specifications. Statistical indices like Cp and Cpk provide numerical measures of process capability, enabling businesses to assess if their processes are capable of producing quality outputs consistently. For example, a bakery may use capability analysis to determine if their cookie production meets size standards.
Continuous Improvement
SPC promotes ongoing improvement. By continually analyzing data and making gradual adjustments, companies can enhance processes, leading to better efficiency and product quality.
Benefits of Implementing SPC
Integrating SPC into your operations can offer substantial advantages:
Improved Product Quality
Regular monitoring processes helps identify deviations from quality standards. For instance, a pharmaceutical company found through SPC that their error rate in pill counting dropped by 30% within six months of implementation.
Cost Reduction
Implementing SPC reduces waste and defects, translating to significant savings. A study found companies that adopted SPC reduced their costs by as much as 25% by minimizing rework and scrap.
Enhanced Customer Satisfaction
Delivering quality products consistently builds customer loyalty. A retail company discovered that maintaining quality through SPC increased their customer satisfaction scores from 75% to 90% in just one year.
Data-Driven Decision Making
SPC fosters a strong data-driven culture, putting teams in a position to make informed decisions based on accurate information instead of guesswork.
Increased Efficiency
By identifying and addressing inefficiencies, organizations can optimize operations, leading to higher productivity. A manufacturing firm reported a 15% increase in production efficiency within three months of implementing SPC.
Implementing SPC in Your Organization
Starting SPC requires careful planning. Here’s how to effectively incorporate SPC into your company:
Identify Critical Processes
Determine which processes most critically affect product quality and customer satisfaction. Focus SPC efforts on these areas. For example, if a food service company identifies preparation times as crucial, it should prioritize those processes.
Train Staff
Provide staff training on SPC principles. Empowering your team with the right skills is essential for a successful rollout.
Establish Control Charts
Create control charts for the identified processes to monitor performance consistently. For instance, a call center might set up charts to track call duration, helping to ensure service quality.
Analyze Data
Regularly analyze the collected data. Look for patterns or trends, such as frequent delays in a service process that might indicate the need for a workflow adjustment.
Implement Changes
Act on the data analysis to make necessary corrections. If you notice a significant rise in defects, consider modifying the production process to address the root cause.
Foster a Culture of Continuous Improvement
Encourage a mindset of ongoing improvement among all team members. SPC should be seen as an ongoing journey rather than a one-time project.
Common Challenges in SPC Implementation
While the benefits of SPC are clear, challenges can arise:
Resistance to Change
Staff may be hesitant to change their ways. Address their concerns and highlight SPC’s benefits to ease this transition.
Data Management
Efficient data collection is crucial for effective SPC. Organizations need robust systems in place to manage relevant data accurately.
Lack of Expertise
A solid understanding of statistical methods is vital. Consider investing in training or hiring experts to guide initial implementation.
Balancing Costs and Benefits
An organization may worry about the immediate costs of implementing SPC. Careful planning and illustrating long-term benefits can help justify these investments.
Case Study: Successful Implementation of SPC
To demonstrate the power of SPC, let’s look at a prominent automotive manufacturer. They faced declining product quality and rising customer complaints, prompting them to adopt SPC techniques.
Overview
Management pinpointed several key manufacturing processes that directly influenced product quality. Employee training on SPC principles was rolled out, followed by the establishment of control charts for critical processes.
Implementation
During the implementation, ongoing data collection and analysis were performed. This allowed them to identify inefficiencies and tackle the root causes of variability.
Results
The results were striking. Product quality improved significantly, revealing a 40% reduction in defects and a 50% increase in customer satisfaction ratings within a year. By instilling a culture of continuous improvement, the company sustained a quality control framework that bolstered their market position.

The Future of SPC
Looking ahead, the future of SPC is bright as technology continues to advance.
Integration with Modern Technologies
Organizations can look forward to combining SPC with real-time data analytics tools. This integration will allow for immediate feedback on process performance, and predictive analytics can help identify potential issues before they escalate.
Greater Emphasis on Continuous Improvement
Continuous improvement will remain integral to SPC. Future endeavors will need to engage more employees beyond quality control in creating a quality-centric culture.
Broader Applications
SPC principles are spreading beyond manufacturing into industries such as healthcare and finance, where the importance of data-driven quality control is increasingly recognized.
The Road Ahead
Statistical Process Control (SPC) is a powerful methodology for elevating quality control across industries. By systematically monitoring processes and relying on data, organizations can achieve superior product quality, significant cost reductions, and enhanced customer satisfaction.
The transition to an SPC-focused framework may come with its challenges, but the benefits far outweigh the initial hurdles. With a commitment to ongoing improvement and the incorporation of emerging technologies, SPC will continue to be a vital resource in managing quality effectively.
Organizations ready to cultivate a focused approach to quality will set themselves apart in the competitive marketplace. Investing in SPC will equip them to navigate industry evolution and stand at the forefront of innovation and excellence.


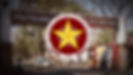